Keliangan, ketakselanjaran jenis rongga yang terbentuk oleh perangkap gas semasa pemejalan, adalah kecacatan biasa tetapi menyusahkan dalam kimpalan MIG dan satu dengan beberapa sebab. Ia boleh muncul dalam aplikasi separa automatik atau robotik dan memerlukan pengalihan keluar dan kerja semula dalam kedua-dua kes — membawa kepada masa henti dan peningkatan kos.
Punca utama keliangan dalam kimpalan keluli ialah nitrogen (N2), yang terlibat dalam kolam kimpalan. Apabila kolam cecair menjadi sejuk, keterlarutan N2 berkurangan dengan ketara dan N2 keluar daripada keluli cair, membentuk buih (liang). Dalam kimpalan tergalvani/galvani, zink yang disejat boleh dikacau ke dalam kolam kimpalan, dan jika tidak ada masa yang cukup untuk melarikan diri sebelum kolam menjadi pejal, ia membentuk keliangan. Untuk kimpalan aluminium, semua keliangan disebabkan oleh hidrogen (H2), dengan cara yang sama seperti N2 berfungsi dalam keluli.
Keliangan kimpalan boleh muncul secara luaran atau dalaman (sering dipanggil keliangan bawah permukaan). Ia juga boleh berkembang pada satu titik pada kimpalan atau sepanjang keseluruhan, mengakibatkan kimpalan yang lemah.
Mengetahui cara mengenal pasti beberapa punca utama keliangan dan cara menyelesaikannya dengan cepat boleh membantu meningkatkan kualiti, produktiviti dan keuntungan.
Liputan Gas Perisai Lemah
Liputan gas pelindung yang lemah adalah punca paling biasa keliangan kimpalan, kerana ia membenarkan gas atmosfera (N2 dan H2) mencemari kolam kimpalan. Kekurangan liputan yang betul boleh berlaku atas beberapa sebab, termasuk tetapi tidak terhad kepada kadar aliran gas pelindung yang lemah, kebocoran dalam saluran gas, atau terlalu banyak aliran udara dalam sel kimpalan. Kelajuan perjalanan yang terlalu pantas juga boleh menjadi punca.
Jika pengendali mengesyaki aliran lemah menyebabkan masalah, cuba laraskan meter aliran gas untuk memastikan kadarnya mencukupi. Apabila menggunakan mod pemindahan semburan, contohnya, aliran 35 hingga 50 kaki padu sejam (cfh) sepatutnya mencukupi. Kimpalan pada amperage yang lebih tinggi memerlukan peningkatan dalam kadar aliran, tetapi adalah penting untuk tidak menetapkan kadar terlalu tinggi. Ini boleh mengakibatkan pergolakan dalam beberapa reka bentuk senjata api yang mengganggu liputan gas pelindung.
Adalah penting untuk ambil perhatian bahawa senapang yang direka bentuk berbeza mempunyai ciri aliran gas yang berbeza (lihat dua contoh di bawah). "Sweet spot" kadar aliran gas untuk reka bentuk atas adalah jauh lebih besar daripada reka bentuk bawah. Ini adalah sesuatu yang perlu dipertimbangkan oleh jurutera kimpalan semasa menyediakan sel kimpalan.
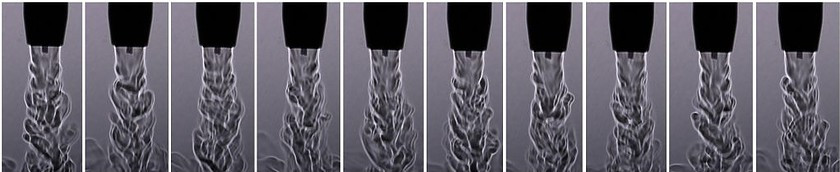
Reka bentuk 1 menunjukkan aliran gas yang lancar pada alur keluar muncung
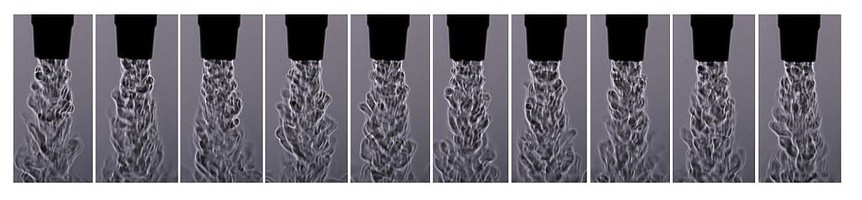
Reka bentuk 2 menunjukkan aliran gas bergelora di alur keluar muncung.
Periksa juga kerosakan pada hos gas, kelengkapan dan penyambung, serta gelang-O pada pin kuasa pistol kimpalan MIG. Gantikan jika perlu.
Apabila menggunakan kipas untuk menyejukkan operator atau bahagian dalam sel kimpalan, berhati-hati supaya ia tidak dihalakan terus ke kawasan kimpalan yang boleh mengganggu liputan gas. Letakkan skrin di dalam sel kimpalan untuk melindungi daripada aliran udara luar.
Sentuh semula program dalam aplikasi robot untuk memastikan terdapat jarak hujung ke kerja yang betul, yang biasanya ½ hingga 3/4 inci, bergantung pada panjang lengkok yang dikehendaki.
Akhir sekali, kelajuan perjalanan perlahan jika keliangan berterusan atau rujuk pembekal pistol MIG untuk komponen bahagian hadapan yang berbeza dengan penutup gas yang lebih baik
Pencemaran Logam Asas
Pencemaran logam asas adalah satu lagi sebab keliangan berlaku — daripada minyak dan gris kepada skala kilang dan karat. Kelembapan juga boleh menggalakkan ketakselanjaran ini, terutamanya dalam kimpalan aluminium. Jenis bahan cemar ini biasanya membawa kepada keliangan luaran yang boleh dilihat oleh pengendali. Keluli tergalvani lebih terdedah kepada keliangan bawah permukaan.
Untuk memerangi keliangan luaran, pastikan untuk membersihkan bahan asas dengan teliti sebelum mengimpal dan pertimbangkan untuk menggunakan dawai kimpalan berteras logam. Kawat jenis ini mempunyai tahap penyahoksida yang lebih tinggi daripada wayar pepejal, jadi ia lebih tahan terhadap sebarang bahan cemar yang tinggal pada bahan asas. Sentiasa simpan wayar ini dan mana-mana wayar lain di kawasan kering dan bersih dengan suhu yang serupa atau lebih tinggi sedikit daripada loji. Melakukan ini akan membantu meminimumkan pemeluwapan yang boleh memasukkan lembapan ke dalam kolam kimpalan dan menyebabkan keliangan. Jangan simpan wayar di dalam gudang sejuk atau di luar rumah.
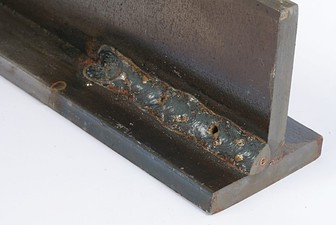
Keliangan, ketakselanjaran jenis rongga yang terbentuk oleh perangkap gas semasa pemejalan, adalah kecacatan biasa tetapi menyusahkan dalam kimpalan MIG dan satu dengan beberapa sebab.
Apabila mengimpal keluli tergalvani, zink mengewap pada suhu yang lebih rendah daripada keluli cair, dan kelajuan perjalanan yang pantas cenderung membuat kolam kimpalan membeku dengan cepat. Ini boleh memerangkap wap zink dalam keluli, mengakibatkan keliangan. Lawan keadaan ini dengan memantau kelajuan perjalanan. Sekali lagi, pertimbangkan wayar berteras logam (formula fluks) direka khas yang menggalakkan pelepasan wap zink dari kolam kimpalan.
Nozel Tersumbat dan/atau Bersaiz Kecil
Muncung tersumbat dan/atau bersaiz kecil juga boleh menyebabkan keliangan. Percikan kimpalan boleh terkumpul di dalam muncung dan pada permukaan hujung sentuhan dan penyebar yang membawa kepada aliran gas pelindung yang terhad atau menyebabkan ia menjadi bergelora. Kedua-dua situasi meninggalkan kolam kimpalan dengan perlindungan yang tidak mencukupi.
Menggabungkan keadaan ini ialah muncung yang terlalu kecil untuk aplikasi dan lebih terdedah kepada pembentukan percikan yang lebih besar dan lebih cepat. Muncung yang lebih kecil boleh memberikan akses sambungan yang lebih baik, tetapi juga menghalang aliran gas kerana kawasan keratan rentas yang lebih kecil dibenarkan untuk aliran gas. Sentiasa ingat pembolehubah hujung sentuhan ke muncung lekat (atau ceruk), kerana ini boleh menjadi satu lagi faktor yang mempengaruhi melindungi aliran gas dan keliangan dengan pemilihan muncung anda.
Dengan itu, pastikan muncung cukup besar untuk aplikasi. Biasanya, aplikasi dengan arus kimpalan tinggi menggunakan saiz wayar yang lebih besar memerlukan muncung dengan saiz lubang yang lebih besar.
Dalam aplikasi kimpalan separa automatik, semak percikan kimpalan secara berkala dalam muncung dan keluarkan menggunakan playar pengimpal (welpers) atau gantikan muncung jika perlu. Semasa pemeriksaan ini, sahkan bahawa hujung sentuhan berada dalam keadaan baik dan peresap gas mempunyai port gas yang jelas. Operator juga boleh menggunakan kompaun anti-percikan, tetapi mereka mesti berhati-hati untuk tidak mencelupkan muncung ke dalam kompaun terlalu jauh atau terlalu lama, kerana jumlah kompaun yang berlebihan boleh mencemarkan gas pelindung dan merosakkan penebat muncung.
Dalam operasi kimpalan robotik, melabur dalam stesen pembersihan muncung atau reamer untuk memerangi pembentukan percikan. Peranti ini membersihkan muncung dan penyebar semasa jeda rutin dalam pengeluaran supaya ia tidak menjejaskan masa kitaran. Stesen pembersihan muncung bertujuan untuk berfungsi bersama-sama dengan penyembur anti percikan, yang menggunakan lapisan nipis kompaun pada komponen hadapan. Terlalu banyak atau terlalu sedikit cecair anti percikan boleh mengakibatkan keliangan tambahan. Menambahkan letupan udara pada proses pembersihan muncung juga boleh membantu dalam membersihkan percikan longgar daripada bahan habis pakai.
Mengekalkan kualiti dan produktiviti
Dengan berhati-hati untuk memantau proses kimpalan dan mengetahui punca keliangan, ia agak mudah untuk melaksanakan penyelesaian. Melakukannya boleh membantu memastikan lebih banyak masa arka, hasil yang berkualiti dan lebih banyak bahagian yang baik bergerak melalui pengeluaran.
Masa siaran: Feb-02-2020